- X-ray Tubes
- Multilayer Optics
- Microfocus Source IµS
ixtubes – Microfocus X-ray Sealed Tube Sources Manufactured by Incoatec
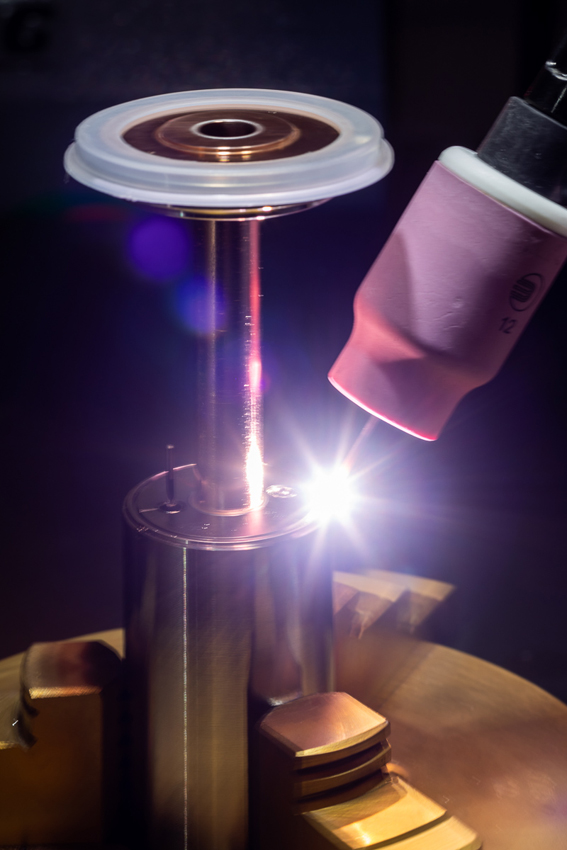
The concept of using a microfocus X-ray sealed tube source in combination with X-ray optics for diffraction experiments was first pioneered by U. Arndt (MRC-LMB, Cambridge) in the early 90’s. However, despite its impressive intensity, this first-generation microfocus source found limited acceptance due to relatively poor stability and very short tube lifetimes. Since then, there have been numerous research activities for finding suitable combinations of high-brilliant microfocusing sealed tube X-ray sources and X-ray optics. With respect to the X-ray optics, a breakthrough was the development of graded multilayer mirrors by H. Goebel (Siemens AG) in the mid 90’s. Multilayer mirrors have proven to be excellent beam-shaping devices for preserving the brightness of the microfocus X-ray source, resulting in a high intensity and good spectral purity. However, all microfocus X-ray tubes used for diffraction experiments at that time had in common that they were standard microfocus X-ray tubes, primarily designed for applications in non-destructive testing. This is because such tubes were readily available from several manufacturers, as non-destructive testing represents a much bigger industrial market compared to the market volume for X-ray diffraction instrumentation. Further, it is by no means easy to develop and manufacture a high-quality X-ray source, as one needs a sophisticated infrastructure and very specialized know-how. Therefore, it is not surprising that little to no efforts have been made so far for optimizing a microfocus X-ray source itself to match the requirements of the applications in diffraction. This is the main reason why Incoatec invested in establishing its own microfocus sealed tube development and manufacturing division IXT.
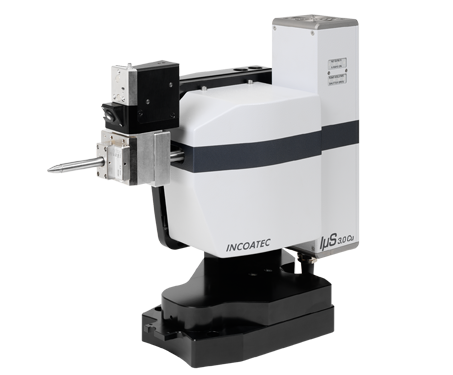
The Incoatec Microfocus Source IµS – Superb Performance and Proven Reliability
Incoatec’s microfocus source IµS consists of a low-power microfocus sealed tube which is combined with a state-of-the-art Montel multilayer mirror for 2D beam shaping. Since its introduction in 2006, the IµS has become the market-leading microfocus sealed tube X-ray source for many X-ray diffraction applications, such as protein and small molecule crystallography, high pressure research, microdiffraction, 2-dimensional X-ray diffraction (XRD2) and small angle X-ray scattering. Up to now, more than 1500 IµS sources have been sold and installed world-wide in academia and industry.
While the original 30 W IµS and the IµSHigh Brilliance contain third-party tubes designed primarily for NDT applications, the IµS 3.0 and the IµS DIAMOND II contain dedicated tubes which are optimized for diffraction and are “Made in Geesthacht”.
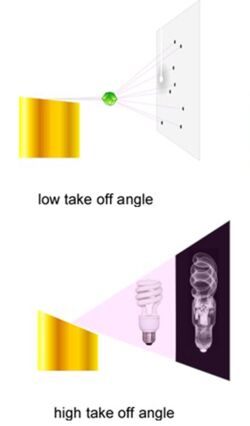
The ixtube – The First Masterpiece from Incoatec’s Tube Factory IXT
Over the past few years, Incoatec’s IXT team has subsequently explored and optimized several parameters critical to the performance of the source in X-ray diffraction applications, such as the take-off angle, e-beam focusing and filament shape. In a typical NDT tube operated in reflection mode, usually the footprint of the electron beam is very small, and the take-off angle is rather large (typically in the range of 20 to 50°, sometimes even larger), giving a large field of view required for radiography of larger objects.
However, for applications in X-ray diffraction, the source needs to “illuminate” only a small volume, as the typical sample sizes are in the range of a few mm down to a few µm. Thus, there is no need for a large field of view. One of the most important aspects for diffraction experiments is getting maximum intensity on the sample. Additionally, the X-ray beam needs to be monochromatic for most diffraction experiments, which requires the X-ray tube to be coupled to an X-ray optics that only filters the Ka radiation of the characteristic spectrum of the anode material pass. Multilayer X-ray optics have proven to be very efficient when it comes to monochromatize an X-ray beam while preserving most of the brilliance of the X-ray source. Due to the limited intrinsic view angle of a multilayer, a multilayer mirror typically “sees” only source sizes in the range of about 100 µm and smaller, which make them the perfect X-ray optics for microfocus sources.
The intensity of an X-ray tube can be increased by exciting a larger footprint on the anode by using an electron beam which is slightly elongated along the beam direction. In order to keep the apparent spot size of the X-ray tube small and tailored to the small acceptance angles of the multilayer optics, the take-off angle needs to be reduced, yielding a “concentrated” X-ray beam with a large number of photons within a solid angle (i.e. a high apparent brightness of the beam). However, the decrease in the take-off angle is limited by the increased self-absorption at lower take-off angles. Due to the small dimensions of the tube, forced air-cooling is sufficient to remove all waste heat.

This dedicated tube design is incorporated in our ixtube series for the IµS 3.0 making it the first tube that is optimized for crystallography. The IµS 3.0 is the 3rd generation of the IµS, yielding more than twice the intensity of other microfocus sealed tube sources on the market. Apart from the unique X-ray tube design, the mechanics, electronics and beam path have also been optimized to maximize the benefits for the user. The mechanical separation of tube and optics, and the reduction of the tolerance chain in the source mount makes the alignment extremly easy.
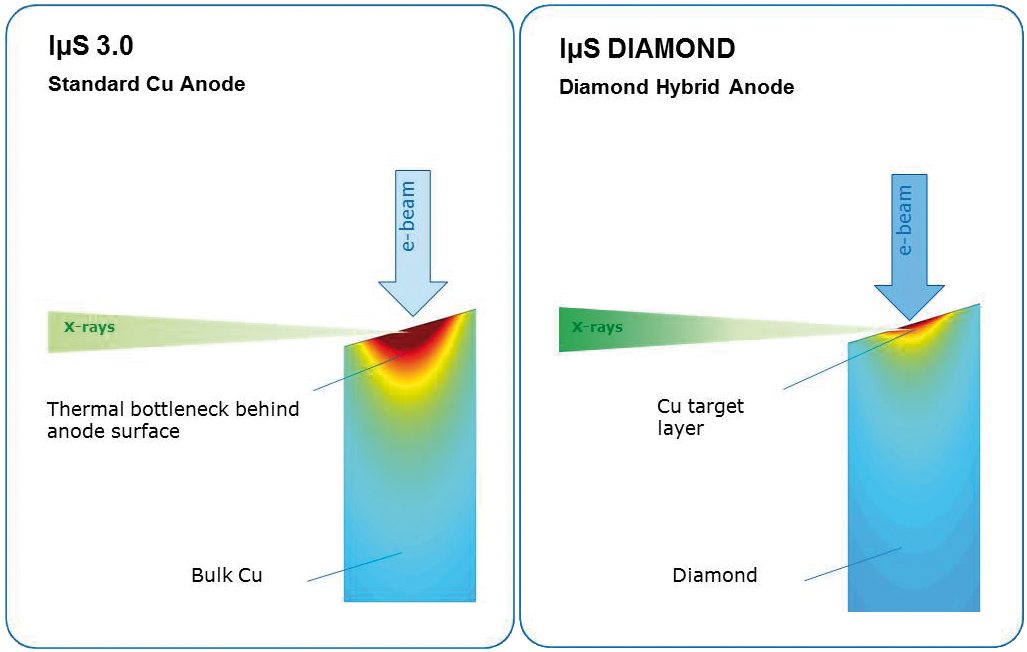
Shine Bright like a Diamond – The Diamond Hybrid Anode
The latest development in Incoatec’s X-ray tube factory is a new type of microfocus sealed tube with a unique anode technology, the diamond hybrid anode.
The diamond hybrid anode consists of an industrial diamond as heat spreader which is coated with a thin layer of the target material (e.g. Cu, Mo, Ag). It takes advantage of the exceptionally high thermal conductivity of diamond, which is up to 5 times higher than thermal conductivity of copper and the highest known conductivity of all bulk materials. This unique property of diamond makes it the material of choice for the thermal management in challenging applications where a high local heat load needs to be dissipated, such as in heat sinks for modern high-power microelectronic devices.
In the ixtube for the IµS DIAMOND II, the thin layer of the target material produces the X-rays while the underlying diamond substrate dissipates the heat load significantly more efficiently than a conventional bulk copper anode, as shown in the right figure comparing simulations of the heat dissipation. Consequently, the diamond hybrid anode can accept a higher power density in the focal spot on the anode without damaging the surface of the target layer, thus, generating more X-rays.
In order to exploit the full potential of the diamond hybrid anode, we have combined the diamond hybrid anode technology with a new high-brightness cathode delivering a dense electron beam with a very high emission rate. This new cathode has an extremely long lifetime beyond that of a classical W filament and is coupled with an active electron lens creating a very bright and uniform footprint on the anode. The IµS DIAMOND II delivers a superb intensity with an intensity gain of up to a factor of about two compared to the previous version of the IμS DIAMOND. The active electron lens is used to focus or defocus the electron beam, e.g. into a stand-by mode, while keeping the power constant. Thereby, thermal load changes between operational mode and stand-by mode are avoided, which will increase the lifetime of the tube.
Multilayer Optics - the Physics Behind
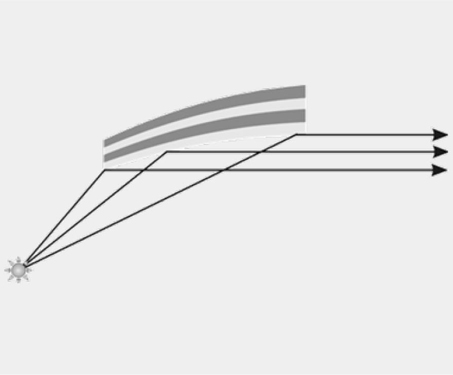
A large variety of thin film based reflective optics exists for home-lab X-ray instruments [1,2] and synchrotrons [3,4]. The most widespread optics at synchrotrons are total reflection optics, where a single layer reflects the incident beam under total reflection, i.e. under a very small angle, typically below 2°, yielding a high flux but low spectral purity. On the other hand, Bragg diffraction on single crystals is used for achieving an excellent monochromatizing and shaping of X-ray beams. Nowadays, Multilayer optics are increasingly replacing single crystal monochromators for conditioning the synchrotron beam in a defined manner. A significant benefit of multilayer mirrors is that the reflection profile of the multilayer film can be designed exactly to the user’s requirements allowing for the tuning of the energy spectrum of the reflected beam.
In home laboratories, highly brilliant microfocus X-ray sources with small focal spots on the anode are combined with multilayer optics for delivering an intensive and monochromatic X-ray beam with a beam cross-section tailored to the size of a typical sample. The multilayer optics is reflecting a monochromatic beam that will either be focused or highly collimated, delivering a high intensity at the sample position while keeping the background scattering small.
For X-ray radiation, the refractive index n = 1-δ+iβ consists of the dispersion δ and the absorption β. As the real part δ of the refractive index n is nearly 1, an X-ray beam cannot be refracted by using a single regular lens. However, an X-ray beam can be conditioned by using a diffractive X-ray optics, such as a multilayer mirror, following Bragg’s law.
According to Bragg’s law, radiation of a certain wavelength, which illuminates a periodic structure with a lattice constant d, is deflected under an angle θ, the so-called Bragg angle. Different orders m of the wavelength are deflected under different angles. The perfection of the lattice as well as the materials forming the lattice are determining the reflectivity R of the periodic structure.
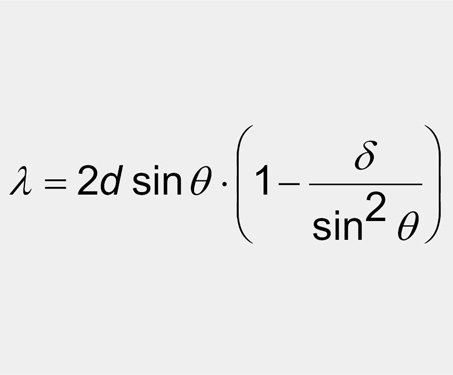
Periodic structures of high reflectivity with tailored d-values can be obtained by multilayer deposition. These multilayers can consist of up to several hundred layer-pairs of two materials with single layers of a few nanometers thickness. The first order (m=1) typically shows a very high reflectivity of up to 95%, and its peak width and energy bandwidth can be 1-2 orders of magnitude larger than for single crystal optics, yielding a beam with higher intensity and broader energy bandpass. The multilayers consist of alternating layers of a heavier element material as reflector and a light element material as spacer, usually with a high dispersion contrast at the interface. For a good X-ray multilayer optics, the absorption should be low to achieve a high reflectivity and reasonably sharp Bragg reflections.
Using multilayer structures with a lateral gradient in the layer thickness that are deposited onto curved substrates, X-ray optical elements can be formed that reflect, monochromatize and shape an X-ray beam. An example of such an X-ray optical element is the so-called Goebel mirror that consists of a parabolically shaped substrate that is coated with a multilayer film with d-values typically in the range 3 – 5 nm. Due to the parabolical shape in conjunction with the lateral gradient of the d-spacing, the polychromatic divergent beam emitted from an X-ray source is transformed into a monochromatic parallel beam using Bragg diffraction.
References
[1] M. Schuster, H. Göbel, L. Brügemann, D. Bahr, F. Burgäzy, C. Michaelsen, M. Störmer, P. Ricardo, R. Dietsch, T. Holz, H. Mai, “Laterally graded multilayer optics for x-ray analysis” Proc. SPIE 3767, (1999) 183
[2] C. Michaelsen, J. Wiesmann, C. Hoffmann, K. Wulf, L. Brügemann, A. Storm, “Recent developments of multilayer mirror optics for laboratorary x-ray instrumentation”, Proc. SPIE 4782 (2002) 143
[3] M. Störmer, A. Liard-Cloup, F. Felten, S. Jacobi, B. Steeg, J. Feldhaus, R. Bormann, “Investigations of large x-ray optics for free electron lasers”, Proc. SPIE 5533 (2004) 58
[4] B. Steeg, L. Juha, J. Feldhaus, S. Jacobi, R. Sobierajski, C. Michaelsen, A. Andrejczuk, J. Krzywinski, “Total reflection amorphous carbon mirrors for vacuum ultraviolet free electron lasers“, Appl. Phys. Lett. 5, 84 (2004) 657
Production and Characterization of Multilayer Optics
The production of a multilayer mirror can be divided into two major steps: The shaping of the substrate and the deposition of the multilayer coating on the substrate.
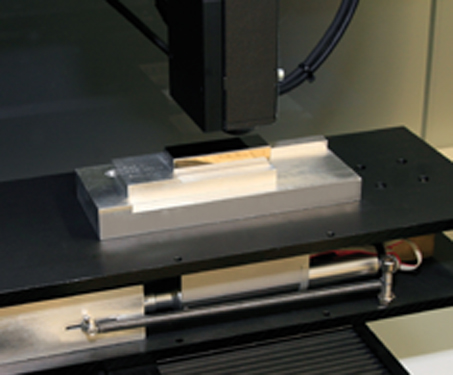
The Substrates
For synchrotron applications, we use perfectly shaped prefigured substrates with ultra-low roughness. For most of the optics for lab-instrumentation, the manufacturing process includes the preparation of substrates by bending silicon wafers into a predetermined shape using dedicated bending tools. The quality of the shape of each substrate is controlled by optical profilometry methods measusuring the peak-to-valley deviation which quantifies the figure error, i.e. fit of the bent substrate to the theoretical shape of the specific mirror design. This deviation in height onto the substrate must be within several hundreds of nanometers.
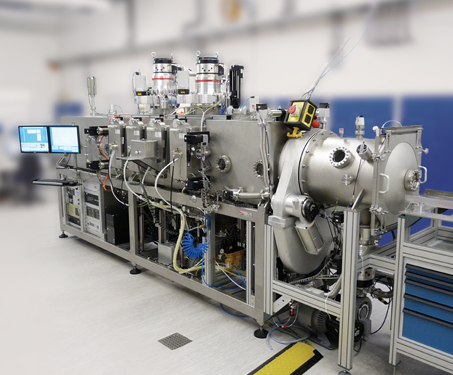
The Deposition
The most important part of the optics production is the deposition of the multilayer coating. We use the very reliable and reproducible method of magnetron sputtering for depositing the multilayer structure that typically consist of two layers - a reflector and a spacer layer - with up to several hundreds of layer-pairs.
We have gathered experience in magnetron sputtering of multilayer structures for over thirty years now, using many different material combinations for single layer or multilayer coatings, e.g.:
C, B4C, BN, SiC, Sc, Ti, V, Cr, Ni, Ge, Mo, Ru, Rh, Pd, La, Ta, W, PT, Au, Ru/C, Cr/B4C, W/Si, La/B4C, Mo/B4C, …
We can deposit stripes of single layer films up to a length of 150 cm, as well as laterally and depth graded multilayers over a length of up to 50 cm.
The multilayer coatings deposited with magnetron sputtering are characterized by an excellent homogeneity, a very good adhesion, high density, low roughness, and high reflectivity.
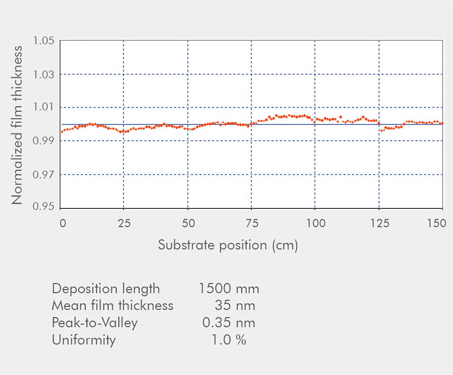
The Characterization
All our multilayer mirrors are extensively characterized for optimum quality control. Typically, coating parameters such as layer thickness, uniformity, density, roughness, reflectivity and gamma ratio for the multilayers are characterized using X-ray reflectometry (XRR) at Cu-Kα (8.0 keV) at several representative positions on each multilayer coating.
The quantification of the 1st Bragg order allows the determination of the maximum reflectivity, integral intensity, and energy resolution of the multilayers. The XRR measurements further allow determining the interface roughness and the material density of the layers. For assuring a high-quality multilayer film deposition and, hence, creating an excellent X-ray mirror, it is crucial to obtain interfaces which are as sharp and smooth as possible, and to achieve optimal density contrast between single layers. The Bragg peak angles can be used to calculate the double layer thickness period, the so-called d-spacing.
The distribution of the d-spacing along the substrate must be within the strict specification of ±1%. This means that we need a precision in thickness along the substrate within the pm range. During the development of new multilayer structures, transmission electron microscopy is employed to measure the quality of the layer interfaces and to investigate whether unwanted interdiffusion between the layers or high roughness of the layers is occurring.
The IµS - The Incoatec Microfocus Source
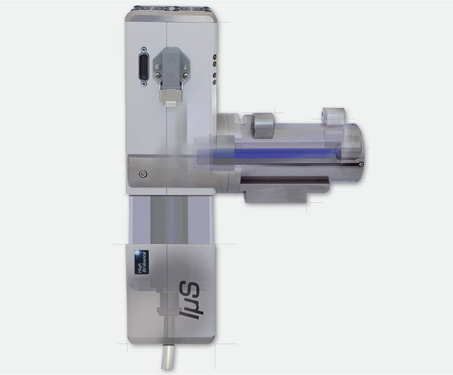
The Perfect Match – Multilayer Mirrors and Microfocus Sources
The IµS is a high-brilliant X-ray source which combines:
- a dedicated high quality multilayer optics and
- a high performance microfocus sealed X-ray tube, including an appropriate high voltage generator
The IµS is compliant with strictest safety guidelines, such as the Machinery Directive 2006/42/EC. It is fully implemented into the software and safety system of Bruker AXS D8 instruments.
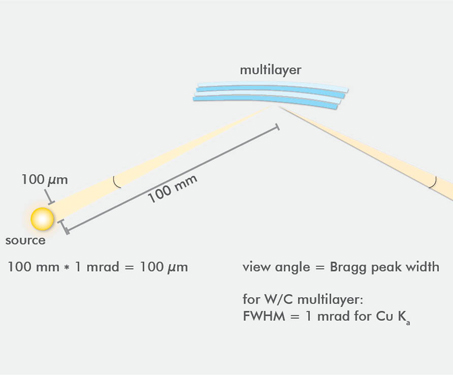
Multilayer Optics - the Main Principle
Multilayer optics are best suited for beam shaping and monochromatization of X-rays. X-rays coming from a polychromatic source are collected by a multilayer structure in a solid angle of approximately 1 mrad and are redirected with a reflectivity larger than 80 % for the Kα-radiation, while simultaneously suppressing all other wavelengths including the Kβ-radiation. To achieve this monochromatization, it requires that the multilayer structure has a lateral gradient of the layer thickness, i.e. the d-spacing, in order to fulfill Bragg‘s law for the varying incident angles at every position of the multilayer mirror along the beam direction. For creating a focused beam after the multilayer mirror, the substrate needs to have an elliptical shape. A collimation into a parallel beam is achieved with a parabolically shaped substrate, as used for the so called Goebel mirrors in certain XRD appliactions. By combining two multilayer mirrors side-by-side in an L-shape, a conditioning of the beam is achieved in 2 dimensions. This assembly is called Montel optics, and is commonly used in applications, such as single crystal diffraction (SC-XRD), small angle scattering (SAXS), micro-diffraction and 2-dimensional XRD (XRD2). In this Montel geometry, the resulting X-ray beam is reflected on each of the two multilayer structures and, thus, the monochromatization effect is squared.
The graphic illustrates that the multilayer optics are an ideal combination for X-ray sources with a focal spot diameter well below 100 µm on the anode. With larger sources, the range of incident angles increases. Therefore, the multilayer optics can only reflect the incident beam partially as the other X-rays do not fulfil Bragg‘s law.
In general, the multilayer optics can easily be designed to fulfill the customer‘s needs. Hence, there are optics having e.g. low divergencies or high flux densities with resulting beam cross-section varying from a few mm down to several tens of µm.
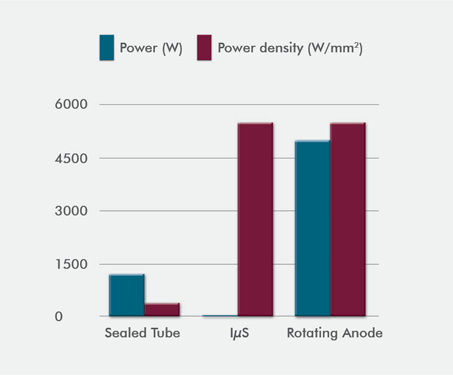
Microfocus Tube - the Main Principle
The IµS provides a highly brilliant X-ray beam in a power range of 10-50 W. It reaches an superb performance by using an air-cooled microfocus sealed tube which has a focal spot of the electron beam on the anode of about 20-50 µm in diameter. Incoatec offers all typical anode materials, such as Cu, Mo, Ag and Cr.
Due to the larger surface-to-volume ratio for the focal spot on the anode compared to the old 1-2 kW sealed tubes, the microfocus sealed tube benefits from an improved heat dissipation and, thus, allows significantly higher power densities. With values larger than 5 kW/mm2, the performance of the IµS is comparable to 5 kW-class rotating anodes (see graphic).
As the brilliance of an X-ray source cannot be increased by the optics, it is, therefore, of utmost importance to achieve the highest possible brilliance for the tube itself. Consequently, it is essential to combine the tube with an optics that conserves the most of the tube’s brilliance. Unlike other types of optics, multilayer optics are a perfect match with microfocus tubes, as they ensure that the small focal spot from the tube is directed to the sample with the minimum losses in brilliance.
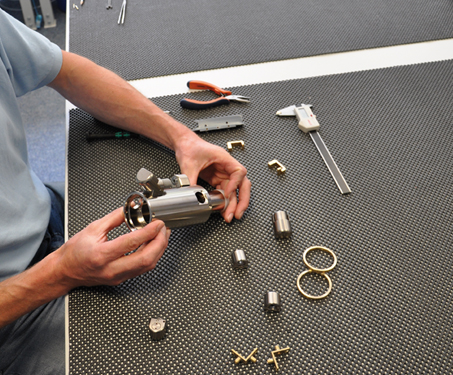
The IµS - Production & Characterization
The secret of the IµS is that the production and assembly of all key components are carried out in-house. The IµS is equipped with the latest generation of Montel Optics, which can be up to 15 cm in length. The multilayer optics are mounted and pre-aligned in our patented optics housing guaranteeing highest stability in beam flux and position.
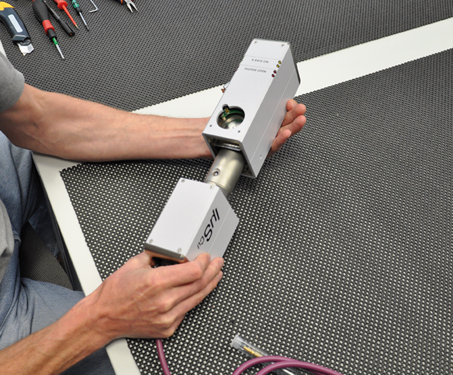
The IµS consists of two parts: first, an X-ray tube mounted and aligned in a cooling body inside a radiation-tight tube housing and, second, an upper housing part containing the fans, the electronic controls and the safety shutter system. The picture left shows how these two parts are assembled. Due to the very efficient air-cooling and the low weight of the IµS, it is possible to mount it on all common goniometers and positioning stages with little effort, allowing an easy customer-specific integration into existing setups. Such IµS upgrades have been successfully installed for more than 100 customers.
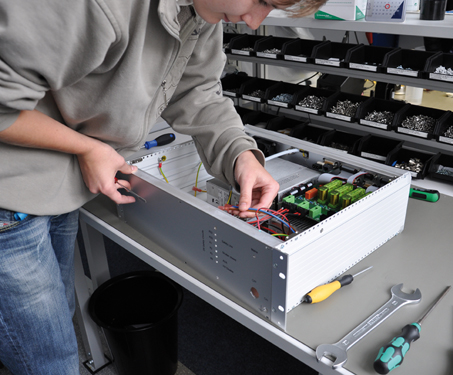
For the electronic control of the IµS an intelligent X-ray generator has been developed by Incoatec.
From the first IµS model on, we have implemented a sensor inside the IµS that closes and locks the shutter of the source in case the optics housing is vented, as the brilliant X-ray beam could otherwise damage the multilayer coating by producing highly reactive ozone. The HV generator for the IµSHigh-Brilliance, IµS 3.0 and IµS DIAMOND are even more advanced as it collects additional information on the properties of the tube and the optics. Parameters such as the ramp rate and maximum operation power of the tube or system failures are monitored and logged. This monitoring system ensures a better and faster customer support. Furthermore, for safety reasons, the shutter between source and optics can only be opened if the optics housing is mounted correctly.
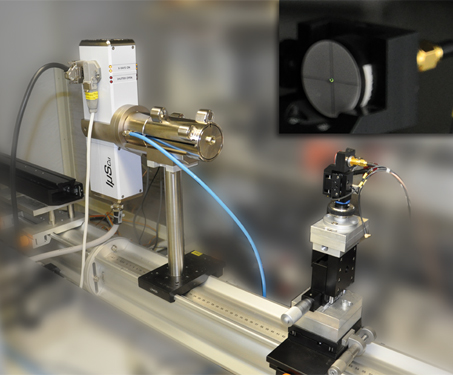
After manufacturing, every IµS is tested in our X-ray lab. The beam profile is checked with a CCD camera and the flux and intensity of the beam are measured with a calibrated diode. These values are the benchmarks which then need to be achieved at the customer’s site after the IµS has been installed.
Having control over the complete production chain ensures that every single IµS is most accurately manufactured and characterized before leaving our company. Our in-house development ensures that the IµS product range is continuously improved, making the IµS the most competitive the market-leading microfocus X-ray source for diffraction.